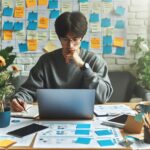
Lean Manufacturing no Controle de Operação Industrial: Mitos e Verdades
Você já olhou para sua linha de produção e se perguntou como poderia extrair mais eficiência dela? Talvez você tenha ouvido falar em Lean Manufacturing, mas não sabe exatamente o que é ou como pode ser aplicado na sua operação. Não se preocupe, você não está sozinho. Muitas empresas ainda têm dúvidas sobre essa filosofia de gestão que promete revolucionar o modo como produzimos.
Neste artigo, vamos mergulhar fundo no Lean Manufacturing, desvendando seus mistérios, benefícios e desafios. Vamos separar o joio do trigo e desmascarar os mitos que cercam essa abordagem. Preparado? Vamos lá!
O Que é Lean Manufacturing?
O Lean Manufacturing, ou Produção Enxuta, é uma abordagem focada na eliminação de desperdícios em todos os processos de uma organização. Seu objetivo principal é entregar o máximo valor ao cliente com o mínimo de recursos. Essa filosofia surgiu nas linhas de produção da Toyota, mas rapidamente se espalhou pelo mundo, conquistando empresas de diversos setores.
A Origem do Lean
O Lean Manufacturing nasceu da necessidade da Toyota de se recuperar da Segunda Guerra Mundial. Com recursos escassos, a empresa precisou encontrar maneiras de otimizar sua produção. Foi assim que o fundador da Toyota, Kiichiro Toyoda, juntamente com seu engenheiro chefe, Taiichi Ohno, desenvolveram um sistema de produção eficiente que ficou conhecido como Toyota Production System (TPS).
Princípios Fundamentais do Lean
O Lean se baseia em cinco princípios fundamentais:
- Especificar o valor: Identificar o que realmente agrega valor para o cliente é o primeiro passo para eliminar atividades desnecessárias.
- Mapear o fluxo de valor: Visualizar todo o processo de produção, desde a matéria-prima até o produto final, para identificar desperdícios e oportunidades de melhoria.
- Criar fluxo contínuo: Eliminar interrupções e gargalos no fluxo de produção, fazendo com que os produtos fluam suavemente.
- Estabelecer um pull system: Produzir apenas o necessário, quando necessário, evitando a produção em excesso.
- Buscar a perfeição: Implementar uma cultura de melhoria contínua, onde todos os colaboradores estão envolvidos na busca por eliminar desperdícios.
Benefícios do Lean Manufacturing
A adoção do Lean Manufacturing traz uma série de benefícios para as empresas:
Redução de Desperdícios
O Lean é sinônimo de eliminar desperdícios. Desde o estoque excessivo até os movimentos desnecessários dos funcionários, tudo o que não agrega valor ao produto final é considerado desperdício e deve ser eliminado.
Aumento da Produtividade
Ao otimizar processos e eliminar desperdícios, as empresas conseguem produzir mais com menos recursos, aumentando significativamente sua produtividade.
Melhoria da Qualidade
O foco na prevenção de erros e defeitos é um pilar fundamental do Lean. Com isso, as empresas conseguem entregar produtos e serviços de maior qualidade, aumentando a satisfação do cliente.
Flexibilidade e Adaptabilidade
O Lean ajuda as empresas a se tornarem mais ágeis e flexíveis, capazes de responder rapidamente às mudanças do mercado.
Satisfação do Cliente
Ao entregar produtos e serviços com maior qualidade, rapidez e menor custo, as empresas aumentam a satisfação dos clientes e fortalecem sua relação com eles.
Mitos Comuns Sobre o Lean Manufacturing
Apesar dos inúmeros benefícios, o Lean Manufacturing ainda é cercado por alguns mitos que podem desencorajar sua implementação. Vamos desmistificar alguns deles:
Mito 1: Lean é Apenas para Grandes Empresas
Um dos maiores equívocos é pensar que o Lean é exclusivo para grandes corporações. Na verdade, empresas de todos os portes podem se beneficiar dessa filosofia. Pequenas e médias empresas muitas vezes são mais ágeis e conseguem implementar mudanças mais rapidamente. O segredo está em adaptar os princípios do Lean ao tamanho e complexidade da operação.
Mito 2: Implementar Lean é Caro e Complexo
É verdade que implementar o Lean pode exigir investimentos iniciais, como treinamento e consultoria. No entanto, os benefícios a longo prazo, como redução de custos e aumento da eficiência, superam esses gastos. Além disso, muitas ferramentas e técnicas Lean são simples e podem ser implementadas com poucos recursos.
Mito 3: Lean Significa Cortes de Pessoal
Um dos maiores temores é que o Lean leve a demissões em massa. Isso é completamente falso. O objetivo do Lean não é reduzir o número de funcionários, mas otimizar o uso dos recursos humanos. Na verdade, muitas vezes, o Lean leva a um aumento da satisfação dos colaboradores, pois cria um ambiente de trabalho mais eficiente e desafiador.
Ferramentas e Técnicas Lean
Para alcançar os objetivos do Lean, é necessário utilizar um conjunto de ferramentas e técnicas. Vamos conhecer algumas das principais:
5S: Organização e Limpeza
O 5S é uma metodologia japonesa que visa criar um ambiente de trabalho organizado, limpo e seguro. As cinco etapas são: Seiri (senso de utilização), Seiton (organização), Seiso (limpeza), Seiketsu (padronização) e Shitsuke (disciplina).
- Liderança 5S: A Chave para a Transformação Cultural e a Excelência Operacional
- Como o 5S contribui para a eliminação do desperdício?: Aumentando a Produtividade e a Eficiência
Kanban: Controle do Fluxo de Produção
Kanban é um sistema visual que ajuda a gerenciar o fluxo de trabalho. Utilizando cartões ou sinais, é possível controlar a produção de acordo com a demanda, evitando excesso de estoque.
Just-in-Time (JIT): Produção Sob Demanda
O JIT é uma estratégia de produção que busca produzir apenas o necessário, quando necessário. Isso reduz estoques, minimiza desperdícios e aumenta a velocidade de resposta às mudanças de mercado.
Mapeamento do Fluxo de Valor (VSM): Visualização do Processo
O VSM é uma ferramenta gráfica que permite visualizar todo o fluxo de valor de um produto ou serviço, desde a matéria-prima até o cliente final. Identifica desperdícios e oportunidades de melhoria.
Kaizen: Melhoria Contínua
Kaizen é a filosofia de melhoria contínua, onde todos os colaboradores estão envolvidos na busca por aperfeiçoamento constante. Pequenas mudanças podem gerar grandes resultados.
Desafios na Implementação do Lean
Embora o Lean ofereça inúmeros benefícios, sua implementação não é isenta de desafios. Compreender essas dificuldades é essencial para superar obstáculos e garantir o sucesso do projeto.
Resistência à Mudança
Uma das principais barreiras é a resistência à mudança. Muitas vezes, os colaboradores estão acostumados com a forma como as coisas são feitas e podem resistir a novas ideias e métodos. É fundamental envolver os funcionários no processo de mudança, explicando os benefícios do Lean e como isso impactará positivamente seus trabalhos.
Falta de Comprometimento da Liderança
O apoio da liderança é crucial para o sucesso do Lean. Se os líderes não estiverem comprometidos com a filosofia, será difícil criar uma cultura Lean na empresa. É necessário que a alta gestão esteja envolvida em todas as etapas do processo, dando suporte e incentivando a equipe.
Cultura Organizacional
A cultura organizacional também pode ser um desafio. Algumas empresas possuem uma cultura burocrática ou hierárquica, o que pode dificultar a implementação do Lean, que valoriza a autonomia e o trabalho em equipe. É preciso criar uma cultura de colaboração, aprendizado contínuo e melhoria constante.
Casos de Sucesso do Lean Manufacturing
Para inspirar e mostrar a aplicabilidade do Lean em diferentes contextos, vamos analisar alguns casos de sucesso:
Toyota: A Pioneira
A Toyota é o exemplo mais conhecido de sucesso com o Lean Manufacturing. A empresa enfrentou desafios após a Segunda Guerra Mundial e encontrou na filosofia Lean a solução para se recuperar e se tornar uma líder mundial na indústria automotiva. A Toyota demonstrou que o Lean pode ser aplicado em larga escala e gerar resultados extraordinários.
Casos de Sucesso em Pequenas e Médias Empresas
O Lean não é exclusivo das grandes corporações. Muitas pequenas e médias empresas também alcançaram resultados impressionantes com a implementação do Lean. Por exemplo, uma fábrica de móveis conseguiu reduzir o lead time de produção em 50% e aumentar a produtividade em 30% através da aplicação dos princípios Lean.
O Futuro do Lean Manufacturing
O Lean Manufacturing é uma filosofia dinâmica que evolui constantemente. Algumas tendências importantes para o futuro incluem:
Lean e Indústria 4.0
A convergência do Lean com a Indústria 4.0 promete revolucionar a produção. A combinação de tecnologias como IoT, inteligência artificial e realidade aumentada com os princípios Lean pode levar a níveis ainda mais altos de eficiência e flexibilidade.
Sustentabilidade e Lean
A preocupação com a sustentabilidade está cada vez mais presente nas empresas. O Lean pode contribuir significativamente para a redução do impacto ambiental, ao eliminar desperdícios e otimizar o uso de recursos.
Conclusão
O Lean Manufacturing é uma jornada de melhoria contínua que pode transformar radicalmente a forma como uma empresa opera. Ao eliminar desperdícios, otimizar processos e focar na satisfação do cliente, o Lean proporciona uma série de benefícios que vão desde a redução de custos até o aumento da competitividade.
É importante ressaltar que a implementação do Lean requer dedicação, persistência e o envolvimento de todos os colaboradores. Não se trata apenas de aplicar ferramentas e técnicas, mas de mudar a cultura organizacional.
Embora existam desafios, os resultados alcançados por empresas que adotaram o Lean são inspiradores. O futuro do Lean está ligado à integração com novas tecnologias e à busca por uma produção mais sustentável.
Perguntas Frequentes
1. O Lean Manufacturing é adequado para empresas de serviços?
Sim, o Lean pode ser aplicado em diversos setores, incluindo serviços. O foco na eliminação de desperdícios e na criação de valor para o cliente é válido para qualquer tipo de negócio.
2. Quanto tempo leva para implementar o Lean Manufacturing?
O tempo de implementação varia de acordo com o tamanho da empresa, complexidade dos processos e nível de comprometimento. Alguns resultados podem ser vistos rapidamente, enquanto outras mudanças podem levar mais tempo.
3. Quais são os principais indicadores de desempenho (KPIs) para medir o sucesso do Lean?
Alguns KPIs relevantes incluem redução de lead time, redução de estoques, aumento da produtividade, redução de defeitos, aumento da satisfação do cliente e retorno sobre o investimento (ROI).
4. É possível implementar o Lean Manufacturing gradualmente?
Sim, é possível iniciar a implementação do Lean em etapas. Começar por um processo ou área específica pode ser uma boa estratégia para obter resultados rápidos e gerar motivação para continuar o projeto.
5. Como envolver os colaboradores na implementação do Lean?
A participação dos colaboradores é fundamental para o sucesso do Lean. É importante envolvê-los desde o início, explicar os benefícios, ouvir suas ideias e reconhecer suas contribuições. Treinamentos e programas de sugestões também são importantes.
Este artigo é apenas um ponto de partida para sua jornada Lean. Existem muitos recursos disponíveis, como livros, artigos, cursos e consultorias, que podem ajudá-lo a aprofundar seus conhecimentos e implementar o Lean com sucesso em sua empresa.